Closed forging
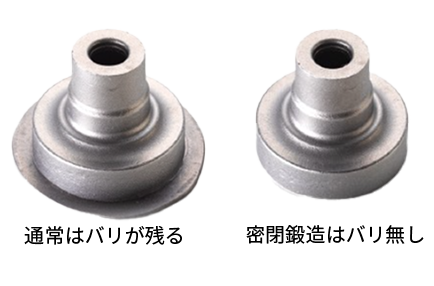
There is no burr. So costs are reduced.
Closed forging is a forging method that uses only materials of almost the same mass as the finished form. Normal forging adjusts the weight so that the material comes out of the mold, but the portion that came out of this method becomes "burr" and must be removed in the post-process.
In the case of closed forging, the mass is controlled not to make materials come out of the mold, so that the material cost for burrs can be saved.
Advantages of Closed forging
- Reduced manufacturing time due to no need for trimming process
- Reduced machining time due to less draft angle
- Material cost reduction to reduce material consumption
- Reducing material losses and contributing to the global environment
Specifications for Closed forging
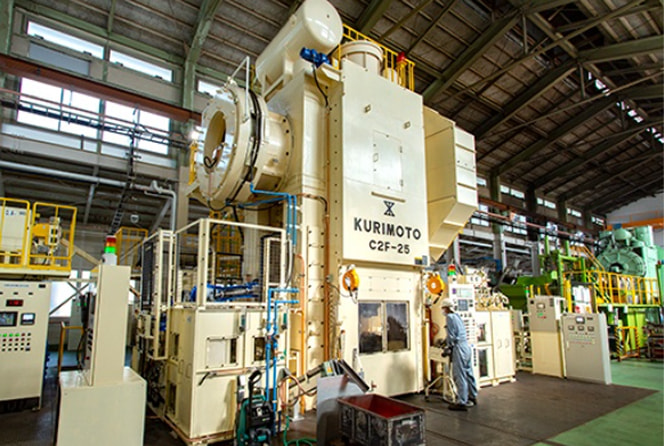
2,500T auto crank press line
We have a 2,500-ton automatic line as a closed forging facility. Automation enables 24-hour operation, so mass production is also possible. Since the weight management of materials is the most important aspect of closed forging, we run a severe management system by utilizing our experience in conventional forging technology.
●Features
- Automation through transfer
- Material loading robot arm enables vertical and horizontal striking.
- Automation enables 24-hour operation.
- Normalizing process is provided as standard on production line.
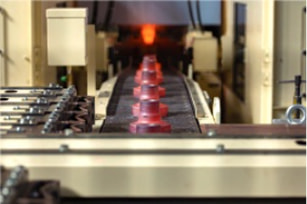
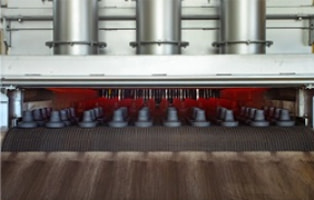
●Specifications
- Compatible materials: SS, SC, SCM, SCr
- Size: Material diameter: φ40 to φ60 Material length: 120~280mm
- Lead time: 35 days after order receipt
- Tolerance :±0.5 mm
- Production capacity: 270,000 shots/month